The market coverage of automotive electronic components is expected to continue to grow in the next few years, with active/passive safety systems, enhanced human-machine interfaces (head-up displays, touch screens, etc.) and body convenience features leading the way. It is worth mentioning that the market demand for higher quality cars will drive the growth of high-end car sales. Between 2013 and 2018, China's automotive electronics market is expected to grow the fastest, with a compound annual growth rate expected to reach 3.5%.
This article refers to the address: http://
As the level of automotive electronics continues to increase, automotive systems will become more complex, which will have an impact on the body electronics system, while also providing significant challenges to electronic system architecture definitions and designs with special application requirements/needs:
â— Increased power load, reduced space and weight, will challenge the thermal processing capabilities of printed circuit boards.
• Solid state power switches require simple diagnostics to minimize the number of lines on the printed circuit board and the application resources required.
• The number of lines between ECUs and between the ECU and the electrical load needs to be optimized and minimized to offset the increased number and weight of lines due to overall complexity.
• Electrical harness cross-section and weight also need to be optimized and minimized to offset the increased number and weight of lines due to overall complexity.
â— Standby current needs to be minimized.
â— Reliability needs to be maximized.
Minimization of power density and application microcontroller resources for body control modules
As mentioned earlier, the power density of the body control module itself will increase significantly as the number of loads managed by the body control module increases and the weight and size of the body control module continue to decrease. Therefore, it is important to control system performance, ie monitor load power consumption and printed circuit board/device temperature. It is worth noting that monitoring the power consumption and temperature of each load places higher demands on the computing power of the monitoring application microcontroller.
STMicroelectronics' latest VIPower M0-7 Series High-Side Driver (HSD) improves diagnostic feedback according to application requirements, using an analog output called multi-sensor pin to monitor up to 4 (load) operating current, battery Voltage and device heatsink temperature, microcontroller resources occupy very little. The new high side drive has the following advantages:
• Simplify printed circuit board design by minimizing the number of connections between control and execution stages on external components and printed circuit boards.
â— During the development phase, the printed circuit board heat map analysis is performed by the power device to simplify the function optimization process of the body control module.
â— Check the welding process after the module is manufactured.
◠When the module overheats, the intelligent “distribution†can selectively turn off the relevant load.
â— Enhanced off-state real-time diagnostics (and even abnormal overheating of off-state devices).
Minimize the number of wires and harness sections
According to STMicroelectronics, after the electromechanical relay is replaced by a large number of electronic switches, the cross section of the automotive electrical harness can be reduced by a factor of two, and the amount of insurance used in the body control module is also greatly reduced, saving more space for the printed circuit board. , reduce the weight.
Figure 1 is a typical circuit diagram of a lighting system using relay control.
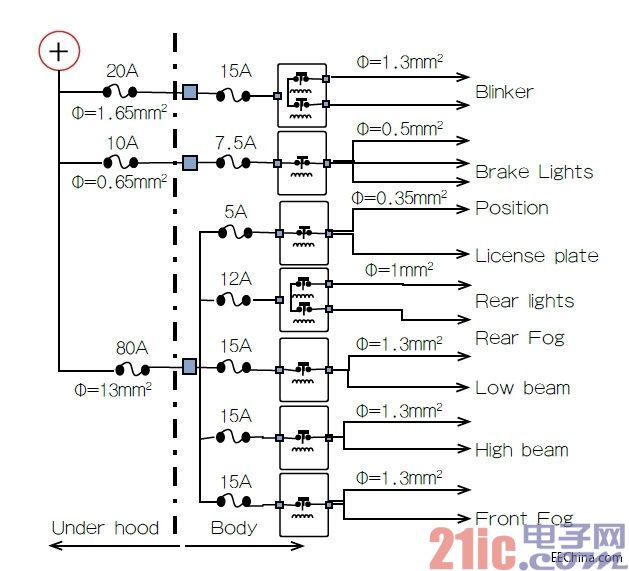
Figure 1: Circuit diagram of the lighting system for relay control.
To minimize the amount of insurance used, it is common practice to centrally install the load to share a single insurance. Considering this problem with two turn signals, it is clear that the selected fuse must be rated to withstand the maximum operating current required for all loads to operate simultaneously (in this example: the maximum operating current is 2 times 21W + 21W + 5W) ). To ensure (15A in this example) a higher short circuit current. Therefore, the wiring design must consider the overall load rather than a single line load. Obviously, this problem can theoretically be solved by an insurance-in-charge method, but this solution has high requirements on cost, weight and space, especially considering the increasing number of automotive convenience loads mentioned above.
Figure 2 shows three current-time curves:
â— A pulse current that can be withstood by a 0.5 mm2 copper wire. This pulse current is a function of the pulse duration.
• The time it takes for the VND7020 to enter the thermal shutdown mode when a pulse current is applied that is a function of the current pulse amplitude.
â— Turn signal load (two 21W bulbs and one 5W bulb) curve (typical).
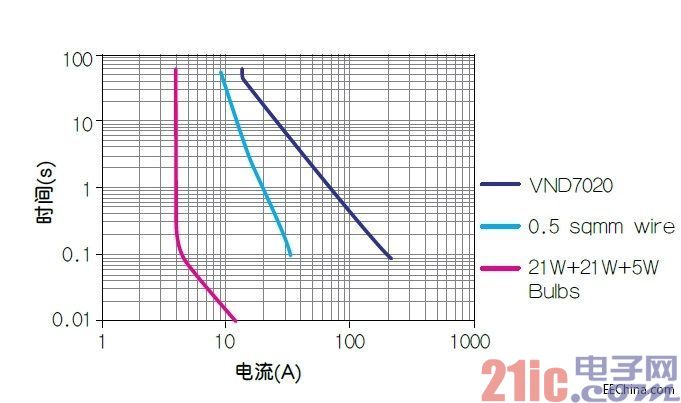
Figure 2: Current-time graph for different states.
As can be seen from the figure, the VND7020 curve is located between the load and the cable curve, indicating that the operating conditions are normal, not entering the thermal shutdown mode, the device can protect the cable when an overload (such as a short circuit) occurs.
Each channel of this multi-channel device has a protection function. The developer can select the cable according to the load characteristics, and the cable can be protected by electronic technology. The insurance can be replaced to further save space, reduce weight and save cost. For example, if a high-side driver is used, the load connection can be modified as shown in Figure 3.
Optimize system cost
In the past few years, the complexity of body control modules and the market-requested system functions have been limited to a limited number of load drives and weaker diagnostic functions, so the pressure to reduce system costs has focused on the drivers required for these few loads. chip. As mentioned earlier, this situation is changing rapidly. The increase in the number of load on the body computer drive and the urgent need for vehicle manufacturers to improve diagnostics and safety have made the automotive system more complex, shifting the focus of cost reduction from pure semiconductors to the total system cost of the car.
On a sizing printed circuit board, increasing module complexity places higher demands on the integration of electronic components. This trend is most evident on smart power switches, where devices must integrate more intelligent functions (such as protection and diagnostics) while compressing the size of the chip and package to minimize printed circuit board size, weight and cost. ST's high-side drivers drive this market trend. Historically, each generation of VIPower-M0 technology has reduced chip size by 40% to 50%, which makes it possible to use smaller packages, such as PowerSSO- 16. The new package measures 20 mm2 and can accommodate multiple M0-7 HSD switches with a single-channel switch on-resistance of at least 10mΩ and a four-channel switch with on-resistance of at least 50mΩ.
Although the chip size is small, the thermal performance is not affected. ST's chip manufacturing technology and packaging technology make the PSSO-16 package have excellent thermal performance (on a 4-layer printed circuit board, the thermal resistance RTH is 21 ° C / W).
From the perspective of lowering total cost of ownership, car companies require that the body electronics system must support modularity (for example, Volkswagen's MQB platform). By enabling car companies to reuse the same printed circuit board in different automotive markets and models, modular solutions can reduce the cost of design, test, and manufacturing, improve product quality, and shorten development cycles.
To meet this requirement, STMicroelectronics' VIPower M0 high-side driver is pin-to-pin compatible with the same generation of products, and the software is compatible with each other. The scalability that appears on the M0-5 product is improved on the M0-7, about 70% of which is The products sold share the same package (PPSO-16), covering different on-resistance values ​​and channel counts (PSSO16 has single or dual channel products). These features improve module reusability by driving different electrical loads through the same printed circuit board design as long as different drivers are soldered during the manufacturing process.
Developers can further reduce the overall development cost of body control modules by using thermal analysis software tools to determine the appropriate printed circuit board size, device selection, and physical positioning. STMicroelectronics has extensive experience in thermal analysis and can provide dedicated load compatibility reporting, load module partitioning support and printed circuit board thermal performance improvements if required by customers.
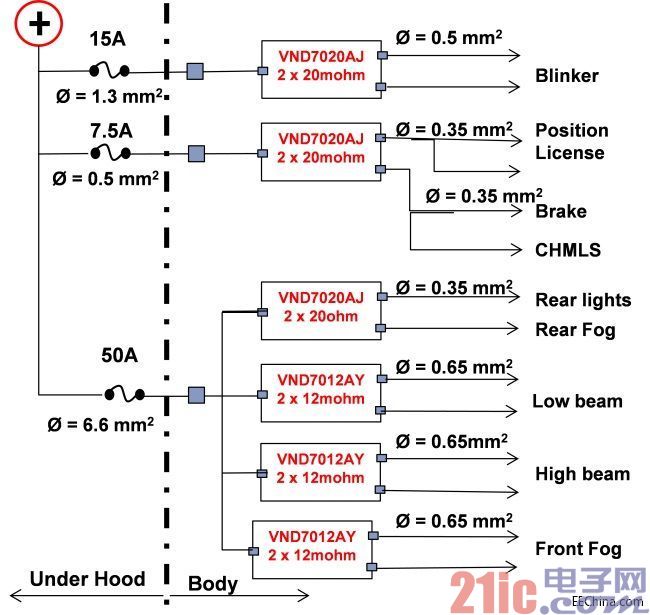
Figure 3: Load connection diagram using a high-side driver.
New application area
Today, different application requirements are the decisive factor in the overall development trend of automotive electronic systems, and also the driving force for semiconductor industry application innovation and product planning. In addition to the special needs arising from the automotive electronics process, as well as the innovative drivers for optimizing system costs, there are new development requirements in terms of industry standards and regulatory requirements, as well as new application areas.
In the field of new body electronics applications. The replacement of halogen lamps and HID lamps by LED light sources has become a major trend in the current automotive market. In addition, the electronic distribution of automotive power distribution boxes is the biggest business opportunity for semiconductor products outside the traditional market.
In today's power distribution boxes, there are usually up to 200 fuses and 30 relays, and the hardware weighs only 1.5 kg. The size of the cable can not be ignored. In addition, traditional insurance requires an intervention time, and the use of such insurance requires the vehicle to select a wiring scheme according to the insurance characteristics rather than the rated load.
STMicroelectronics has taken note of this market trend and has relevant manufacturing technology and research and development capabilities to provide the market with special features (eg low on-resistance, low standby on-state static current) and can replace insurance and relay distribution. solution.
100W Solar Street Lights,100W Solar Led Street Light,Super Bright 100W Solar Street Light,High Lumen 100W Solar Street Light
Yangzhou Bright Solar Solutions Co., Ltd. , https://www.solarlights.pl