In the control system, the HMI is like a “gatekeeperâ€, which prevents the operating personnel from being flooded with large amounts of data and provides a safe operation guide.
The application trends in the automation industry have facilitated the development of HMI, which has helped factories improve process safety and facility operations. Modern HMI's improvements in areas such as human-centered design, graphics configuration, and graphics portability have enabled engineers and operators to work more efficiently.
The core of human-machine interface development is human-centered design research, including teamwork among automation designers, academia and users. The Operational Performance Center is a team that conducts research in this area. Through the research, collaboration, and human factors engineering, this cooperative organization solves the problems of human capabilities and limitations. Through the solid foundation of research and user testing, human-machine interfaces that meet modern requirements are designed.
Designing an HMI from scratch instead of working on a pre-built human-machine interface means fewer configuration reworks and native integration with the system, which can further simplify the workflow of engineers and operators.
The principles of modern HMI design <br> The difference between valid and invalid displays is how the data provides operational information. The design of modern HMI can center on the needs of users and follow the following human-centered design principles to bring higher productivity to users.
Visualization: During the process of interacting with the machine during the shift, what can the operator watch on the screen or not pay attention to? These answers will affect how to overcome automation and process problems, and how to deal with potential, costly mistakes. For example, studies use darker colors in most areas of the screen, and use more vivid colors in abnormal conditions to attract the attention of the operator.
Pattern recognition: The use of the display mode improves the speed and accuracy of the operating personnel's assessment of operating conditions. In the traditional interface, the operator needs to read and compare values. Modern human-machine interfaces use patterns that people are more familiar with, so the display itself becomes information and requires only a small amount of explanation.
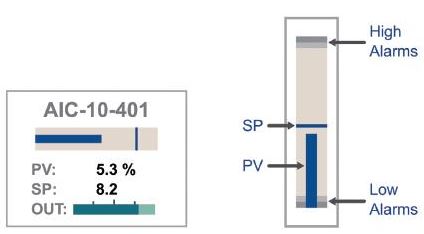
Display Navigation: With the expansion of work areas or control areas, operators often need to browse through hundreds of display pages. The best practice recommended by the Center for Operational Performance and Standards of the International Institute of Automation (ISA) recommends that the display content be designed according to the hierarchical structure of the information according to the device area. The purpose of hierarchical structure is to enable operators to quickly access the required display pages and take appropriate actions.
Unfortunately, the hierarchy is not widely adopted because most HMIs were not designed with hierarchical navigation at the beginning of the design, nor were they effective tools for creating hierarchical displays. Modern HMIs can simplify the creation of hierarchical displays.
Simplified graphics configuration <br> The requirements for control system HMI functions and display complexity are increasing. However, the graphical configuration tools do not keep pace with the need for increased speed - often requiring engineers to use programming languages ​​to create complex graphics solutions. With the continuous development of modern human-machine interfaces, these human-machine interfaces are designed to enable engineers to easily create a human-centered design environment. Note the following factors that will help operators improve productivity and optimize overall operations.
Reduce reliance on scripts: Graphical configurations do not require high software programming techniques to create, adapt, or adapt to different operating concepts. When configuring the display, users expect a more intuitive interface. These displays require very little programming (if any) and can ensure that the project time schedule is met. Human-centered design principles allow for simplification of certain tasks, such as related scripting work, and provide graphical configuration tools that enable complex functions to be implemented without the need for extensive scripting.
Customizable interface: The display page is no longer configured by a specific engineer for all running tasks. The former operator must wait for the engineer to implement the change, and the manufacturer provides the operator with more choices. The engineer can configure the working area of ​​the operator and allow the operator to customize some of the content as needed.
Change Management: Device change and control strategies evolve throughout the life cycle. The display page must be modified accordingly. Modern graphics tools can provide built-in, user-friendly features to reduce the time required to configure the display.
Mobility and Security <br> On displays other than the control room and operator workstations, system information needs to be provided more frequently to meet changing user needs. Workers are now accustomed to mastering information anytime, anywhere, and the display interface needs to meet their needs.
However, more and more attention to network security has brought higher requirements, making it more difficult to control the process of sending control information outside the control room. Modern control systems have added network protection layers and other security protections. Modern mobile solutions are designed based on a more secure architecture that makes it easier to provide viewing access without having to convert the display to a new format.
Older control systems often do not design or install these network security requirements. In response to these security requirements, the remote access display feature was disabled, which was previously accessible. The problem is that factory personnel still need to access these system information.
Modern human-machine interface design embeds mobility into the interface so that it can adapt to changing requirements in different plant environments, and it can be expanded over time. Now, if a portable security display system is used, then in the future when the plant is rebuilt in real time, no redesign is needed at all, and the access capabilities of mobile devices can be increased.
When the control system's human-machine interface meets the needs of operators and engineers, the entire operating activities will naturally improve. Operators can identify problems faster, handle information more easily, and easily adapt to changes. In addition, through human-machine interface improvements, engineers can more easily adopt industry mapping standards and best practices. By improving situational awareness and turning data into useful information, operators can quickly and easily make decisive decisions and the operational process will become safer, more intuitive, and more effective.
Pay more attention to "people" in HMI
Although the human-machine interface begins with the word "human", the HMI's support for the machine is higher than the support for humans from most previous technology histories. It can be said that the adjustment of the way the machine provides information has always been a burden on operators. In recent years, HMI hardware has gradually adopted the user-friendly interface technology that has been popularized in the consumer electronics field, and has been optimized in terms of product quality and screen layout preferences. For many machine manufacturers and end users, the use of plastic low-end HMI devices with a 6-inch single-touch screen is out of date.
The optional industrial HMI hardware includes precision-machined aluminum and steel housings, as well as high-definition widescreen or portrait screens, extending the range of traditional HMIs. Capacitive multi-touch technology has changed the concept of HMI by hardware and software vendors, with more emphasis on the "person" part of the concept.
Now, you can quickly get the information you need by sliding the HMI software on the screen instead of pressing the buttons to access the various screens. With the advent of the HMI software platform, Web development standards such as HTML5 and JavaScript can be integrated and mobile devices can be regarded as HMI hardware. This means that the HMI can be any display with a web browser.
Web-based HMI
For machine operators and technicians, the benefits of Web-based HMIs are that there is no need to stop the work at hand, go back and forth to the HMI display installed in a specific area of ​​the machine to check parameters or retrieve data during debugging, troubleshooting , start or switch. Now, this situation is changing because with the help of smartphones or tablets, the Web-based HMI can be "closely" to factory personnel.
The same principle applies to the concept of a wearable HMI so that even smart watches and data glasses can apply augmented reality to the factory floor. Outside the HMI screen, a communications application has been created that enables push notifications. These applications can send machine operation related messages to all mobile and wearable devices.
Despite the rapid growth of mobile technology in HMI applications, advances in communications technology have not prevented HMI devices from being installed on machines. Using the IoT communication standard, Panel PCs (PC-based controllers with built-in display screens) can send continuous plant and manufacturing data to cloud-based services for viewing and implementing big data analytics across the enterprise . Data is securely pushed to analytic dashboards or provided to web-based pages and viewed by authorized users anytime, anywhere.
(Author: Camilo Fadul)
ZGAR AZ Vape Pods 5.0
ZGAR electronic cigarette uses high-tech R&D, food grade disposable pod device and high-quality raw material. All package designs are Original IP. Our designer team is from Hong Kong. We have very high requirements for product quality, flavors taste and packaging design. The E-liquid is imported, materials are food grade, and assembly plant is medical-grade dust-free workshops.
From production to packaging, the whole system of tracking, efficient and orderly process, achieving daily efficient output. WEIKA pays attention to the details of each process control. The first class dust-free production workshop has passed the GMP food and drug production standard certification, ensuring quality and safety. We choose the products with a traceability system, which can not only effectively track and trace all kinds of data, but also ensure good product quality.
We offer best price, high quality Pods, Pods Touch Screen, Empty Pod System, Pod Vape, Disposable Pod device, E-cigar, Vape Pods to all over the world.
Much Better Vaping Experience!
ZGAR AZ Vape 5.0 Pods,ZGAR AZ Vape Pods 5.0,ZGAR AZ Vape Pods 5.0 Pod System Vape,ZGAR AZ Vape Pods 5.0 Disposable Pod Vape Systems
ZGAR INTERNATIONAL(HK)CO., LIMITED , https://www.zgarvapepen.com